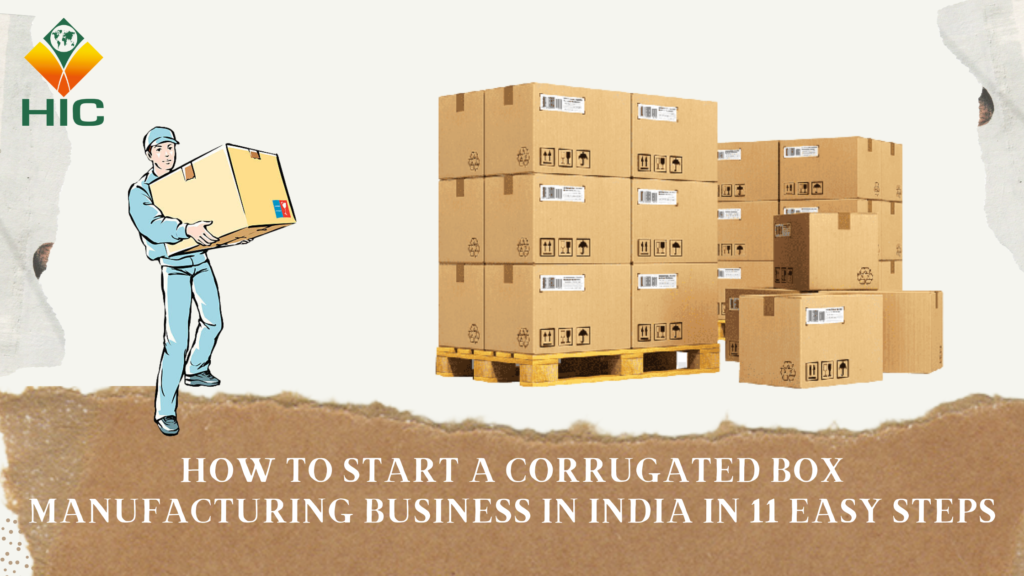
Corrugated Box Manufacturing Business in India | Establishing in 11 Steps
- No Comments
A corrugated box is a type of container that is paper-based, and it is often used to pack goods for shipping. The boxes are rigid and can be folded as they are easy to store and transport. In order to start Corrugated Box Manufacturing Business in India, HIC MACHINERY CO. Guide by following these 11 essential steps will help you How to start Corrugated Box Manufacturing Business in India.
List of 11 mandatory Steps for starting Corrugated Box Manufacturing Business in India:
- Select the best location for your factory
- Make sure all the necessary permissions are available
- Prepare your production unit with the necessary equipment
- Hire skilled workers or train them if necessary
- Learn about the different types of boxes
- Choose from one of the many design templates
- Order packaging materials
- Decide on the best type of packing material to use
- Get an estimate of how many boxes you need to produce every month
- Prepare a marketing plan
- Necessity under the law
Step 1: Select the best location for your factory | Corrugated Box Manufacturing Business In India
You need to decide where you want your factory to be. It is best if it is not too far from a major city. You will need to get all the necessary permissions for your factory and you will also need skilled workers.
Step 2: Make sure all the necessary permissions are available
Before you invest in a corrugated box manufacturing unit, you will need to make sure that all the necessary permissions are available. You will need to take care of the necessary permits for your business and also for the land where you want to set up your factory. It is important to get this sorted out before investing a large sum of money as it involves paying certain fees too.
Step 3: Prepare your production unit with necessary equipment
One of the first steps you will need to take is preparing your production unit with the necessary equipment. These items are important because they will help you stay organized and more efficient:
- To begin with, a Sheet cutter.
- Second, there’s the Sheet Pasting Machine.
- Finally, there’s Eccentric Slotter.
- Next, The Pressing machine is used.
- Then there’s the Variable frequency drive.
- After that, Single Face Corrugating is used.
- In addition, Board Cutter
- Rotary Cutting and Creasing Machines are also available.
- Stitching and Flexo Printing Machines are also available.
- Finally, turn on the generator.
Step 4: Hire skilled workers or train them if necessary
All the steps listed are important for starting a corrugated box manufacturing unit in India, and step 5 is no different. Hiring skilled workers or training them if necessary is an important part of the process. If you don’t have many workers with skills in this area, there are some things you can do to get them trained. This is called up-skilling, which means developing skills that they may not currently have. You could hire someone who has these skills or you could train your current employees in this area. The potential benefits of up-skilling include increased productivity and better quality products being made due to more skilled labor.
Step 5: Learn about the different types of boxes
There are many types of corrugated boxes, but they all have the same basic shape. They can’t stand on their own, but they are very sturdy and durable.
Corrugated boxes come in a variety of sizes and shapes. The most common type is called a “tri-wall box” or “three-ply box,” which is made up of three sheets of corrugated board that is glued together at the edges to form an enclosed space. Sometimes, these boxes will be reinforced with inserts or cross braces.
Step 6:Choose from one of the many design templates
There are many different design templates to choose from when you are designing your corrugated box. Depending on the product that you want to package, you may need a certain type of box. For example, if you sell clothing, a rectangular-shaped box would be ideal because it has space for clothing. But if your business is in the food industry and you want to package fruit or vegetables, then a square shape may work better for your needs.
Step 7:Order packaging materials | Corrugated Box Manufacturing Business In India
One of the most important things to do when starting a corrugated box manufacturing unit in India is to order all the necessary packaging materials. Your packers will need to be able to pack everything neatly and securely, which is why you’ll need packing tape and other items. You’ll want to start by finding out how many boxes you need to produce every month so that you can order the appropriate amount of tape.
Step 8: Decide on the best type of packing material to use
With the rise of online shopping and easier worldwide shipping, the global logistics sector is expanding at a breakneck pace. In 2018, over 65 million boxes and packages were sent worldwide, a figure that has increased every year since.
Since there are so many shipments in the vast global shipping systems, it’s critical that your products arrive in the same condition as you sent them out. Packing and labeling your products correctly helps ensure that you do not lose a lot of money.
This course will help you how to learn about the many materials available and how to determine which ones are ideal for your products.
Using the perfect packing materials for your items will decrease breakages and replacements, save you money, and make your customers happier.
Knowing what materials are available and what to think about when designing packaging will help you create a system that fits your budget and your products.
This tutorial will show you how to learn about the many materials available and how to determine which ones are ideal for your products.
Step 9:Get the right estimate of how Identification of Customer Needs boxes.
The size of the box varies depending on the industry Customer Needs. There are three specification sizes of boxes: small (Mono Cartons), standard (Standard Cartons), and large (Large Cartons). You must know the dimensions of your target customer’s box. You should also be aware of the many types of boxes. Boxes are available 2/3/5/7 ply are Provided by many Manufacturing companies. Worldwide industries use various types of corrugated boxes. The machine requirements fluctuate as the box layer changes.
Step 10: Prepare a marketing plan
Marketing planning is a systematic roadmap that companies use to organize, implement, and track their promotional strategy over time. Separate marketing strategies for various marketing teams within the organization can be included in marketing plans, but they all work toward the same business objectives.
Step 11:. Necessity under the law | Corrugated Box Manufacturing Business In India
In India, running a business is not as simple as it appears. Some legal criteria must be followed by both new and established businesses and startups. Financial laws, tax obligations, and employment law requirements are just a few of the procedures that any business firm in India must follow. Any form of business can be established (Private Limited, Partnership, Limited Liability Partnership, Public Limited Company, Sole Proprietorship).
Some of the items that are required for your production unit included.
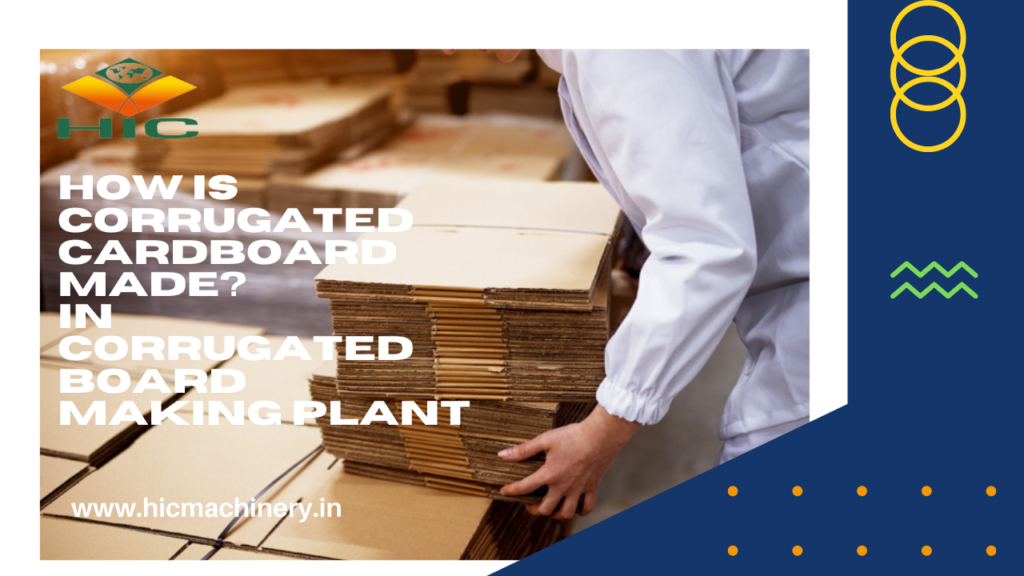
How is corrugated cardboard made? Complete process Overview
- 6 Comments
Welcome to HIC Machinery CO. corrugated, where we manufacture and sell corrugated Automatic plants For 3 PLY & 5 PLY Corrugated boards and a wide range of specialty packaging Corrugated Machines. Today, we’d like to demonstrate how we make our products. The main material of the corrugated board is the containerboard grades of the paper liner which becomes the flat facings of the board is primarily made from the long fibers of softwood trees media format which becomes the fluted middle layer of corrugated board is primarily made from the shorter fibers of hardwood trees. In this Article, We Know The Complete Overview process of Corrugated board-making plant machinery from start to finish HOW IS CORRUGATED CARDBOARD MADE?
HIC Machinery Co. (Top 3/5Ply Corrugated Plant Manufacturer)
HOW IS CORRUGATED CARDBOARD MADE? | The first step in making a corrugated board
The first step in the production of a corrugated board takes place in a machine known as a single phase. A single phaser combines a liner and a medium to make a single face web. To do this, the medium is passed through a set of corrugating rolls at high heat and pressure to form the flutes that give the corrugated board.
The performance attributes needed for the finished packaging item.
Its tensile strength and cushioning capacity Each pair of corrugating rolls is manufactured in a specified flute and profile to provide the performance characteristics required for the finished packaging item. After a cornstarch-based adhesive is applied to the flute tips by the glue roll, the liner is brought into contact with the fluted medium by a pressure roll, which turns against a metering roll to control the proper quantity of adhesive that is provided to the flute tips.
It is critical that the correct pressure is applied to the corrugating rolls and also that the adhesive reaches the ideal temperature and reliability to form a strong bond between the liner and fluted medium; this combination is known as the single-facer web. The web then leaves the single phaser and is elevated to a bridge that transports the web to the double glue unit.
Double backer : Corrugated liner and corrugated medium
The backer on both sides The liner and corrugated medium are fed into the single phaser from opposite sides via a pair of roll stands that are connected by a device known as a splicer.
The splicer allows the machine to change from one roll to another without stopping when the roll is consumed or when a change in paper grade or width is required as roll stock is unwound and heads to the single phaser.
The paper is wrapped around heated rolls or pre-heaters, which heat the paper to the right temperature for the corrugating process. Wrap arms govern the amount of time the paper is exposed to heat, allowing for some control over raising or decreasing heat to the paper.
Single Facer Web : Corrugated Sheets Exporter And supplier | HOW IS CORRUGATED CARDBOARD MADE?
The single face web is tried to carry up and away from the single phaser by incline belts. The web folds up in festoons for the length of the bridge until it enters the end section of the bridge that relates to the triple stack.
This exists to allow the single-face web to cure with a firm bond so the integrity of the flute structure is not interrupted if double wallboard is being made Both single phasers on the corrugator are operational, supplying two single face webs to the bridge for assembly at the double glue unit.
The double glue unit
The single-face web is threaded through heated rolls and into a machine known as the double glue unit, which applies cornstarch-based adhesive to the flute tips. The liner, which will become the corrugated board’s outside facing, is threaded through the heated rolls at the bottom of the triple stack.
The outside or double-faced liner for facades and roofs
As the board is dragged into the double backer, the outside or double-faced liner is bonded to the single face web. The top and bottom belts in the double backer pull the board through the machine, and the double backer has a series of heated plates that continue to transfer heat into the board to cure the adhesive bond. The belts in the double backer pull the board through the wet end of the corrugator and force it to the dry end.
The Role of Slitter score | HOW IS CORRUGATED CARDBOARD MADE?
After passing through the double backer, the combined board is scored, slit, and cut to finishing specifications. It next passes via a shear, which cuts the board in half to allow for order adjustments, and then into a slitter score, which slits the board to the right width and, if necessary, places the scores into the board to the required dimensions. Two independent slitter score portions are shown in this state-of-the-art slitter score. While one portion is preparing for the next order, the other is operating.
When it’s time to change orders, the shear cuts the board in half to produce a small space that allows the slitter score sections to drop in or rise from the board path, allowing the board to align between the top and bottom shafts where the scoring and slitting heads are affixed speed after the board is slipped and scored.
The Section Of the cut-off knife
It keeps going till it reaches the cut-off knife. The cutoff knife cuts the final corrugated sheet to the exact size required. An upper and lower knife is found on most corrugators. So that two distinct orders can be joined to print on the same paper width and grade. There are exit wheels that expel cut sheets onto single-belt conveyors.
The corrugator’s stacker beds accumulate the sheets to the stacker bays. The sheets are stacked and then unloaded on moving belts for stacker operators to do quality checks and prepare for strapping and shipment conversion machines transform corrugated sheets into boxes.
Print design and branding machines | Rotary die cutters and flexo folder gluers
These machines print designs and logos on the boxes and cut them to the right size for their purpose. Machines are divided into two categories. flexo folder gluers and rotary die cutters When the box is finished, the flexo machine glues and folds it, while the rotary die cutter departs.
Unglued and flat rotary die-cut boxes, like pizza boxes, are often molded by hand or wrapped around a product and attached to a customer’s equipment. A rotary die cutter may also manufacture numerous boxes from each sheet, whereas a flexo machine yields.
The lasers and optical sensors | HOW IS CORRUGATED CARDBOARD MADE?
Material is transferred to each machine center onto an in-feed conveyor via a series of lasers and optical sensors called photo eyes, as well as communication between an inventory management system and real-time production scheduling. Automatic transfer carts keep each machine fed with corrugated sheet stock. Each stack is broken down into smaller sections called blocks and shingled individually to a feed table.
The sheets are fed through a series of feed wheels that act in tandem with feed rolls to insert the sheet into the machine. The feed rolls are composed of a soft durometer material to avoid crushing the board. Maintaining board caliper or thickness is critical for total board strength in the end box carried by a vacuum transfer system.
The designs and branding are printed
The sheet through the machine across multiple print sections on a rotary die cutter machine the designs and branding are printed on the bottom of the corrugated sheet stock after the stock moves through the print section it reaches the rotary die cutters there are different cutters for every box type that the factory produces.
The cutters Section
The cutters are made up of two half-cylinders with metal blades embedded in them, as well as foam rubber sections to eject the cut board scrap pieces. The scrap is captured and recycled back to a paper mill for future roll stock production. The scrubber is the next section, and it removes any remaining loose cutouts and rough edges on the cut sheets. The sheets are then shingled once again to slow them down as they approach the stacker.
If the sliced sheets collide with the stacker too forcefully. The stacker beds collect the sheets into stacks, which are then discharged on moving belts for the stacker operators to do quality inspections and prepare the sheets for strapping and shipment. The flexo process begins similarly to that of a rotary die cutter, with stock being put onto the conveyor by an automatic transfer system cart each stack is broken down into blocks in this flexo machine. The printing is done on the top of the sheet.
The stock is transferred to a pre-feeder
As a result, the stock must be inverted and transferred to a pre-feeder. This automation eliminates the need for human inversion where the stacks are inverted. The sheets are then shingled and fed into a feed bed, where feed rolls feed the sheet into the machine. The print plates are positioned on a cylinder, and ink is applied to the print plate via an ink system.
This machine also uses rotary die cuts to transfer the ink to the board as it travels through the machine. However, unlike the rotary only cutter, which may manufacture ma18ny boxes per sheet, it only produces one box per sheet. The scrap is caught and recycled for future roll material on a flexo, and machine glue is applied in preparation for folding.
A high-speed detection system called clear vision
Every box is monitored for glue placement and gap measurements using a high-speed detection technique called clear vision. A high-speed camera is plac18ed at the point of glue application to detect the amount and thickness of glue lines, as well as the measurements of the slots in the front and back of each box. These measurements are compared to a developed standard to predict whether a bad box will be produced as it travels through the machine.
Any out-of-spec box will be coated with UV coating, and the bottom of the bundle will be sprayed as well as the bundle moves down.
The UV coating is detected by a black light on the conveyor system, which causes it to expel. The whole package. So that an operator can find and remove the low-quality box.
The speed of production a doubler | HOW IS CORRUGATED CARDBOARD MADE?
It prior to reaching the customer to account for the speed of production a doubler is used to assist crew members in combining each bundle in preparation for load forming the doubler stacks bundles on top of each other these combined bundles are then assembled into a specific stacking pattern to meet customer needs load tags are inserted into each unit to uniquely identify each load as it is sent to shipping to be made ready for delivery to the customer at the end of another workday you can rest easy knowing that you have the very best corrugated supplier in the industry whether you need corrugated sheets standard corrugated containers or specialty packaging products We hope you’ll read to HOW IS CORRUGATED CARDBOARD MADE? and understand the Complete making process Cardboard Boxes by HIC Machinery Co. ( Top 3/5Ply Corrugated Plant Manufacturer) as your supplier of choice safety sustainability innovation quality customer focus and value creation it’s in our DNA in everything we do.
A video post
- No Comments
India’s fastest manufacture 5Ply Automatic Corrugator Board Making Plant Size -1950 mm HIC MACHINERY CO.
fully Automatic 5ply corrugated board making plant with Design Speed of 150 mtr/min Deckle of 1950 mm Successfully installed and Runing at xpertpack Transport company PVT LTD., Bawal.
We have a wide range of Machines relates to manufacture Corrugated Boxes # Made in India Manufactured & Expert of:
Machinery for paper corrugated Board & Box Making and Paper converters . We deals with-
- 1. 3/5 PLY Automatic Corrugated Board Making Plant
- 2. Hydraulic Shaft less Mill Roll Stand
- 3. High Speed Finger less Single Faces
- 4. Trplex pre heaters
- 5. Over head Bridge
- 6. Baker Unit
- 7. PLC controlled Double baker
- 8. NC cut t – off Helicel
- 9. Up / Down stacker
- 10. Die Punching Machine.
- All other Semi automatic and manual machines.